Kia Picanto: Body / Air Conditioner Refrigerant/Compressor
Repair procedures
Refrigerant System Service Basics (R-134a) |
Refrigerant Recovery
Use
only U.L.-listed service equipment that is certified to meet the
requirements of SAE J2210 when removing HFC-134a (R-134a) from the air
conditioning system.
•
| Air conditioning refrigerant or lubricant vapor can irritate your eyes, nose, or throat. |
•
| Be careful when connecting service equipment. |
•
| Do not breathe in refrigerant or vapor. |
|
If accidental system discharge occurs, ventilate work area before resuming to service.
Additional health and safety information may be obtained from the refrigerant and lubricant manufacturers.
1. | Connect
an R-134a refrigerant Recovery/Recycling/Charging System (A) to the
high-pressure service port (B) and the low-pressure service port (C) as
shown, following the equipment manufacturer's instructions.
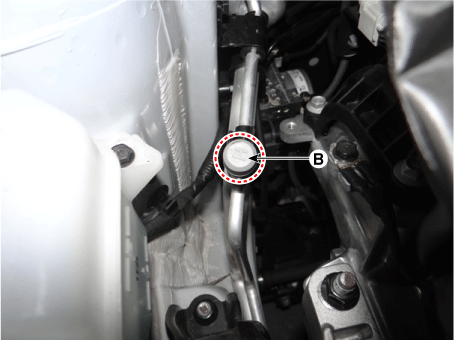
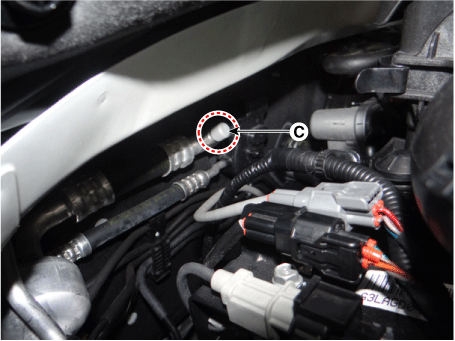
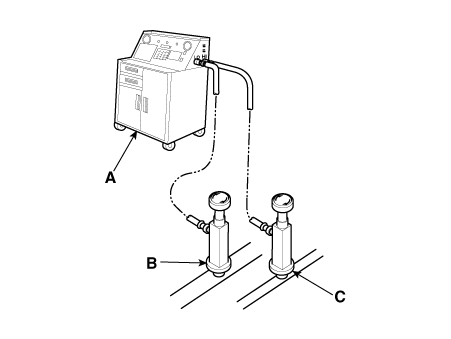 |
2. | Measure
the amount of refrigerant oil removed from the A/C system after the
recovery process is completed. Be sure to install the same amount of new
refrigerant oil back into the A/C system before charging. |
System Evacuation
Use
only U.L.-listed service equipment that is certified to meet the
requirements of SAE J2210 when removing HFC-134a (R-134a) from the air
conditioning system.
•
| Air conditioning refrigerant or lubricant vapor can irritate your eyes, nose, or throat. |
•
| Be careful when connecting service equipment. |
•
| Do not breathe in refrigerant or vapor. |
|
If accidental system discharge occurs, ventilate work area before resuming to service.
Additional health and safety information may be obtained from the refrigerant and lubricant manufacturers.
1. | When
an A/C system has been opened to the atmosphere, such as during
installation or repair, it must be evacuated using a R-134a refrigerant
Recovery/Recycling/Charging system. (If the system has been open for
several days, the receiver/drier should be replaced, and the system
should be evacuated for several hours.) |
2. | Connect
a R-134a refrigerant Recovery/Recycling/Charging system (A) to the
high-pressure service port (B) and the low-pressure service port (C) as
shown, following the equipment manufacturer's instructions.
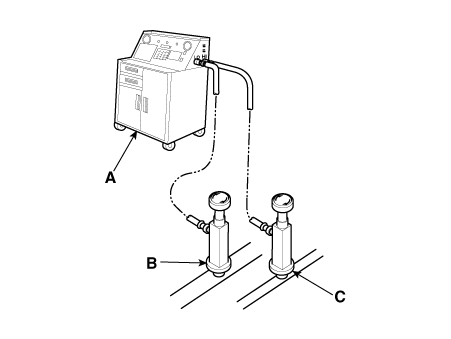 |
3. | If
the low-pressure does not reach more than 93.3 kPa (700 mmHg, 27.6
in.Hg) in 10 minutes, there is probably a leakage in the system.
Partially charge the system, and check for leakage. (See Refrigerant
Leak Test.) |
4. | Remove the low pressure valve from the low-pressure service port. |
System Charging
Use
only U.L.-listed service equipment that is certified to meet the
requirements of SAE J2210 when removing HFC-134a (R-134a) from the air
conditioning system.
•
| Air conditioning refrigerant or lubricant vapor can irritate your eyes, nose, or throat. |
•
| Be careful when connecting service equipment. |
•
| Do not breathe in refrigerant or vapor. |
|
If accidental system discharge occurs, ventilate the work area before resume of service.
Additional health and safety information may be obtained from the refrigerant and lubricant manufacturers.
1. | Connect
an R-134a refrigerant Recovery/Recycling/Charging System (A) to the
high-pressure service port (B) and the low-pressure service port (C) as
shown, following the equipment manufacturer's instructions.
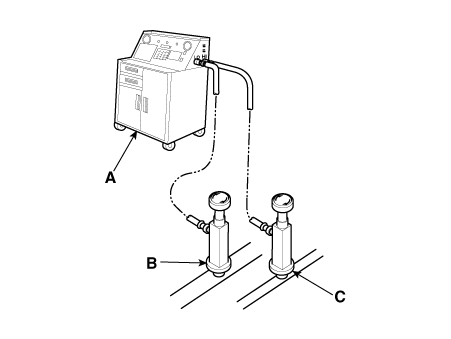 |
2. | Add
the same amount of new refrigerant oil to the system that was removed
during recovery. Use only specified refrigerant oil. Charge the system
with R-134a or R-1234yf refrigerant. Do not overcharge the system as it
may damage the compressor.
Specified amount
400 ± 25g (14.1 ± 0.8 oz.) |
|
Refrigerant Leak Test
Always
conduct a leak test with an electronic leak detector whenever leakage
of refrigerant is suspected and when conducting service operations that
accompany disassembling, loosening or connecting of fittings.
In order to use the leak detector properly, read the manual supplied by the manufacturer. |
If a gas leak is detected, proceed as follows:
1. | Check
the tightening torque of the connection fittings, and if it is too
loose, tighten to the proper torque. Using a leak detector (A), check
for gas leakage. |
2. | If
leakage continues even after the fitting has been tightened, discharge
the refrigerant from the system, disconnect the fittings, and check
their seating faces for damage. Replace at all times even for a slight
damage. |
3. | Check the compressor oil and add oil if required. |
4. | Charge the system and recheck for gas leaks. If no leaks are found, evacuate and charge the system again.
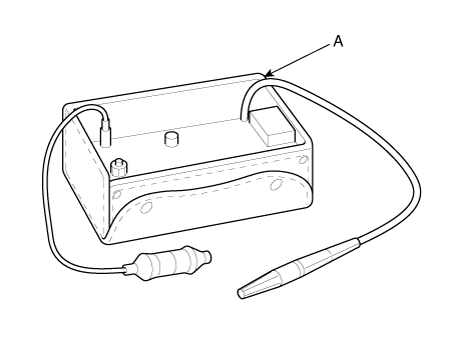 |
Refrigerant System Service Basics (R-1234yf) |
Refrigerant Identification
•
| Do not mix HFO-1234yf (R-1234yf) in the vehicle with other refrigerant, such as R-12, R-134a and etc. |
•
| Use
only service equipment that is U.L-listed and is certified to meet the
requirements of SAE standards to recover and recycle R-1234yf from the
air conditioning system. Do not use service equipment for the other
refrigerant, such as R-12, R-134a and etc. |
•
| Verify
what refrigerant is in the system if there is concern that the system
has been tampered with in any way and check the type and quantity of
refrigerant that shall be in the A/C system and potential issues arising
from accidental or intentional mixing of refrigerants. |
•
| Using
an SAE certified refrigerant identification device is recommended to
prevent improper recovery and the resulting further spread of
contaminated refrigerant, which could potentially damage other A/C
systems and service equipment. Contaminated refrigerant (blend of more
than one refrigerant or non-system refrigerant) in recovery/recycling
equipment could lead to the potential contamination of more refrigerant.
|
•
| Certain
types of electronic leak detection devices (heated diode or corona
discharge) as well as motors, switches, and controls on recovery and
recycling machines, could generate sparks that could serve as ignition
sources in the presence of refrigerants classified as flammable (A2 or
A3) by ASHRAE standard 34 2006. |
•
| It
is possible that the mixing of refrigerants in a A/C system can result
in higher-than-expected system pressures, system and component damage,
diagnostic errors and/or other potential hazards to people and
environment. |
•
| In
case other refrigerant is mixed, recover the contaminated refrigerant
in the A/C system and dispose it in accordance with all applicable
national, regional or local regulations. Clean inside the A/C system
using the specialized detergent and recharge new refrigerant. |
Refrigerant Recovery
Use
only service equipment that is U.L-listed and is certified to meet the
requirements of SAE standards to remove HFO-1234yf (R-1234yf) from the
air conditioning system.
•
| Air conditioning refrigerant or lubricant vapor can irritate your eyes, nose, or throat. |
•
| Be careful when connecting service equipment. |
•
| Do not breathe refrigerant or vapor. |
|
If accidental system discharge occurs, ventilate work area before resume of service.
Additional health and safety information may be obtained from the refrigerant and lubricant manufacturers.
1. | Connect
an R-1234yf refrigerant Recovery/Recycling/Charging System (A) to the
high-pressure service port (B) and the low-pressure service port (C) as
shown, following the equipment manufacturer's instructions.
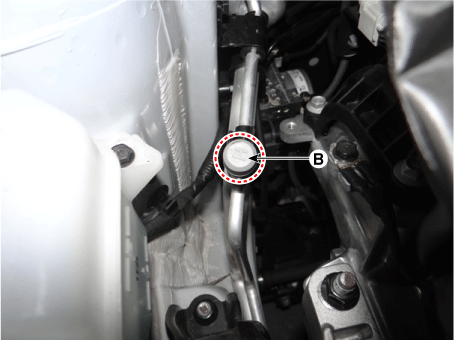
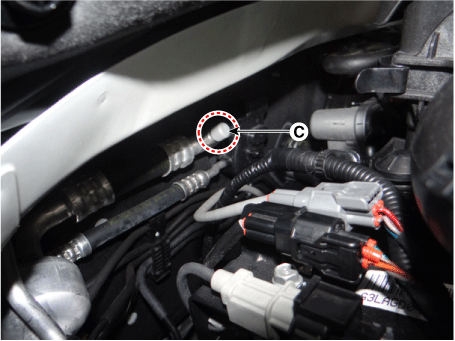
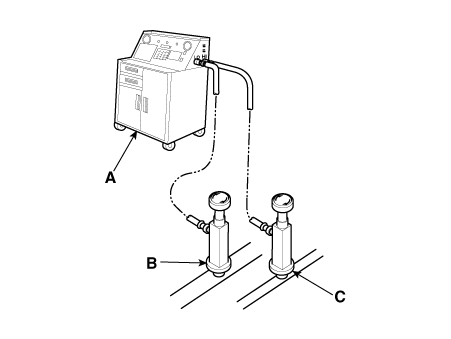 |
2. | Measure
the amount of refrigerant oil removed from the A/C system after the
recovery process is completed. Be sure to install the same amount of new
refrigerant oil back into the A/C system before charging. |
System Evacuation
Use
only service equipment that is U.L-listed and is certified to meet the
requirements of SAE standards to remove HFO-1234yf (R-1234yf) from the
air conditioning system.
•
| Air conditioning refrigerant or lubricant vapor can irritate your eyes, nose, or throat. |
•
| Be careful when connecting service equipment. |
•
| Do not breathe refrigerant or vapor. |
|
If accidental system discharge occurs, ventilate work area before resume of service.
Additional health and safety information may be obtained from the refrigerant and lubricant manufacturers.
1. | When
an A/C System has been opened to the atmosphere, such as during
installation or repair, it must be evacuated using an R-1234yf
refrigerant Recovery/Recycling/Charging System. (If the system has been
open for several days, the receiver/dryer should be replaced, and the
system should be evacuated for several hours.) |
2. | Connect
an R-1234yf refrigerant Recovery/Recycling/Charging System (A) to the
high-pressure service port (B) and the low-pressure service port (C) as
shown, following the equipment manufacturer's instructions.
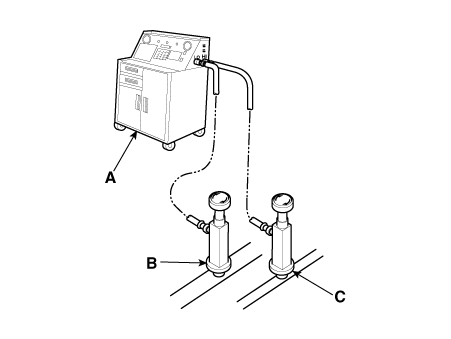 |
3. | If
the low-pressure does not reach more than 87.7 kPa (658 mmHg, 25.9
in.Hg) in 5 minutes, there is probably a leak in the system. Partially
charge the system, and check for leaks (see “Refrigerant Leak Test”). |
4. | Remove the low pressure valve from the low-pressure service port. |
System Charging
Use
only service equipment that is U.L-listed and is certified to meet the
requirements of SAE standards to remove HFO-1234yf (R-1234yf) from the
air conditioning system.
•
| Air conditioning refrigerant or lubricant vapor can irritate your eyes, nose, or throat. |
•
| Be careful when connecting service equipment. |
•
| Do not breathe refrigerant or vapor. |
|
If accidental system discharge occurs, ventilate work area before resume of service.
Additional health and safety information may be obtained from the refrigerant and lubricant manufacturers.
1. | Connect
an R-1234yf refrigerant Recovery/Recycling/Charging System (A) to the
high-pressure service port (B) as shown, following the equipment
manufacturer's instructions.
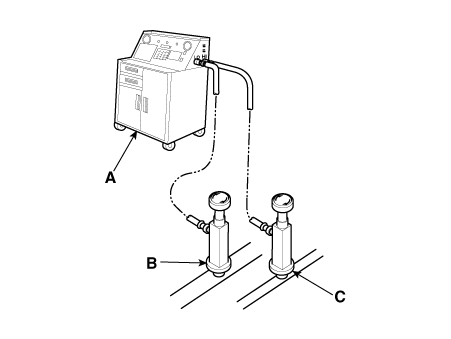 |
2. | Add
the same amount of new refrigerant oil to the system that was removed
during recovery. Use only specified refrigerant oil. Charge the system
with R-134a or R-1234yf refrigerant. Do not overcharge the system as it
may damage the compressor.
Specified amount
400 ± 25g (14.1 ± 0.8 oz.) |
|
Refrigerant Leak Test
Always
conduct a leak test with an electronic leak detector whenever leakage
or refrigerant is suspected and when conducting service operations which
are accompanied by disassembly or loosening or connection fittings.
•
| In order to use the leak detector properly, read the manual supplied by the manufacturer. |
|
•
| Use
only leak detection devices certified to SAE standards for use with
R-1234yf. Certain leak detection devices (heated diode or corona
discharge) could serve as ignition sources in the presence of
hydrocarbons or other flammable refrigerants. |
|
If a gas leak is detected, proceed as follows :
1. | Check
the torque on the connection fittings and, if too loose, tighten to the
proper torque. Check for gas leakage with a leak detector (A). |
2. | If
leakage continues even after the fitting has been tightened, discharge
the refrigerant from the system, disconnect the fittings, and check
their seating faces for damage. Always replace, even if the damage is
slight. |
3. | Check the compressor oil and add oil if required. |
4. | Charge the system and recheck for gas leaks. If no leaks are found, evacuate and charge the system again.
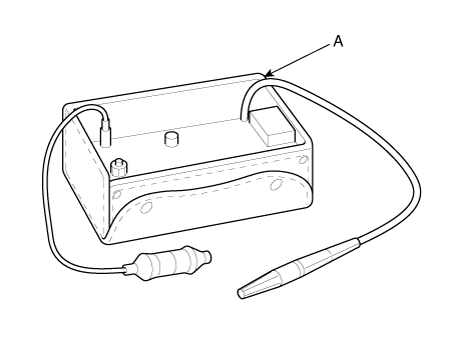 |
RPM check
1. | Push the A/C control switch ON. |
2. | Check the engine RPM. When the compressor operates, RPM increases. |
|
3. | When the compressor is operating, RPM should be as follows. [KAPPA 1.0 MPI]
Ignition Timing
|
BTDC 6° ± 10°
| Idle Speed
| A/CON OFF
| Neutral,N,P-range
| 660 ± 100 rpm
| D-range
| 660 ± 100 rpm
| A/CON ON
| Neutral
| 660 ± 100 rpm
| D, N, P-range
| 660 ± 100 rpm
|
[GAMMA 1.2 MPI]
Ignition Timing
|
BTDC 6° ± 10°
| Idle Speed
| A/CON OFF
| Neutral,N,P-range
| 660 ± 100 rpm
| D-range
| 660 ± 100 rpm
| A/CON ON
| Neutral
| 660 ± 100 rpm
| D, N, P-range
| 660 ± 100 rpm
|
|
Sound check
1. | Push the A/C control switch ON. |
2. | Check the compressor from the engine room. |
3. | When the compressor is operating, a clacking sound is heard. If the compressor isn't operating, there is no sound. |
|
Repair procedures
Filter inspection
The climate control air filter should be replaced according to the maintenance schedule.
If
the vehicle is operated in severely air-polluted cities or on ...
Other information:
To turn on the high beam headlights,
push the lever away from you when
the headlight is on. Pull it back for low
beams.
The high beam indicator will light when
the headlight high beams are switched
on. To prevent the battery from being
discharged, do not leave the lights on
for a pr ...
Seat belt systems should never be disassembled
or modified. In addition, care
should be taken to assure that seat
belts and belt hardware are not damaged
by seat hinges, doors or other
abuse.
WARNING
When you return the rear seatback
to its upright position after
the rear seatba ...